How to Choose the Ideal Pressure Regulator: A Comprehensive Guide for Industrial Efficiency
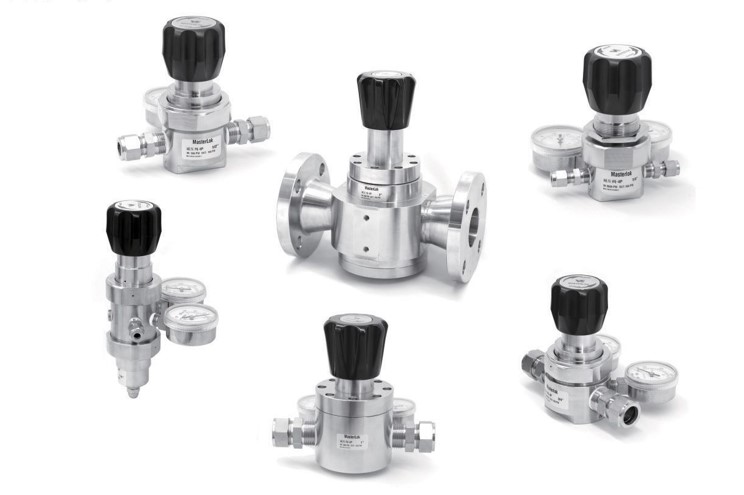
How to Choose the Ideal Pressure Regulator: A Comprehensive Guide for Industrial Efficiency
Selecting an ideal pressure regulator can deliver significant benefits to your operations:
-
Enhanced system efficiency
-
Improved performance
-
Reduced troubleshooting
-
Lower safety risks
A pressure regulator is a device designed to maintain and control gas or fluid pressure. For your system, the ideal pressure regulator depends on your specific process requirements and system design. When selecting a pressure regulator, the following key factors should be considered:
1. Inlet and Outlet Pressure: Defining the Scope of Your Pressure Reducing Valve
Every pressure regulator operates within a specific pressure range, dictated by your system’s upstream (inlet) and downstream (outlet) requirements.
-
High-Pressure Gas Sources: For gas cylinders or LNG storage, a gas pressure regulator must handle extreme inlet pressure fluctuations (e.g., 3000 psi down to near-empty levels).
-
Stable Systems: Downstream applications, like HVAC or medical gas systems, demand precision pressure control valves to maintain consistent output despite inlet variations.
Pro Tip: Always verify the maximum inlet pressure and desired outlet pressure of your system to narrow down valve options.
2. Temperature and Material: Ensuring Durability in Harsh Conditions
Temperature swings and corrosive environments dictate the choice of materials for pressure regulators:
-
Stainless Steel: Ideal for chemical processing or semiconductor-grade ultra-high-purity pressure regulators. Surface treatments like electropolishing and passivation boost corrosion resistance and cleanliness.
-
Specialized Seals: Fluorocarbon (FKM) or PTFE seals are essential for steam pressure regulators exposed to high heat, while cryogenic applications (e.g., LNG at -196°C) require materials resistant to extreme cold.
3.Media Type: Gas, Liquid, or Steam? Match the Regulator to Your Medium
The substance flowing through your system directly impacts valve selection:
-
Gas Regulators: Designed for natural gas, hydrogen, or industrial gases, these often include anti-explosion features.
-
Liquid Pressure Reducing Valves: Prioritize flow stability to prevent water hammer effects in hydraulic systems.
-
Steam Pressure Regulators: Built to withstand high temperatures and pressures, commonly used in boilers or power plants
4. Connection Types: Aligning with Industry Leakage Standards
Leakage rates vary by sector, influencing connection methods:
-
Semiconductor Manufacturing: Welded connections or face seal designs are mandatory for ultra-high-purity regulators to prevent contamination.
-
Oil and Gas Pipelines: Robust NPT (National Pipe Tapered) threads dominate here, balancing high-pressure resilience with ease of installation.
-
General Industry: Flanged or threaded connections offer flexibility for standard pressure control valves.
5. Smart Pressure Regulators: The Future of Fluid Control
With Industry 4.0 revolutionizing industrial automation, smart pressure regulators are gaining traction:
-
Real-Time Monitoring: IoT-enabled valves provide live data on pressure, temperature, and flow rates via digital interfaces.
-
Self-Calibration: Reduces maintenance needs in precision-driven fields like pharmaceuticals or semiconductor fabrication.
-
Energy Efficiency: Adaptive algorithms optimize pressure settings, cutting operational costs in HVAC or compressed air systems.